In industrial environments, proper cable management is essential to maintaining efficiency,
safety, and compliance with industry standards. Cable trays are a critical solution in these
settings, providing support and protection for electrical wiring. From heavy-duty industrial
sites to large commercial facilities, cable trays are used in a wide range of applications to
safely route electrical cables and ensure organized installations.
Types of Cable Trays
- Ladder Cable Trays
Ladder trays are one of the most commonly used systems in industrial settings. They
feature two longitudinal rails with rungs in between, resembling a ladder. This design
allows for excellent ventilation and easy cable access, making them ideal for heavier
cables and environments where heat dissipation is critical, such as data centers and
manufacturing plants. The open design also makes cable inspection and
maintenance straightforward. - Solid Bottom Cable Trays
Solid bottom trays offer complete protection for cables by enclosing them within the
tray. This type of tray is typically used when cables need shielding from dust,
moisture, or other contaminants, making it suitable for indoor installations or
controlled environments. However, they offer limited ventilation, so they may not be
ideal for high-heat applications unless heat-resistant cables are used. - Trough Cable Trays
Trough cable trays offer a balance between the open design of ladder trays and the
protection of solid bottom trays. They have side rails with small perforations or slots
on the bottom, allowing for some air circulation while offering more protection than
ladder trays. This makes them suitable for moderate environments where some
exposure to contaminants is expected, but ventilation is still required. - Wire Mesh Cable Trays
Often used in commercial applications and light industrial settings, wire mesh trays,
also known as basket trays, are made from a grid of wires that form a basket-like
structure. These trays are lightweight and flexible, making them ideal for complex
installations with many changes in direction or elevation. However, they are not
suitable for heavier industrial environments due to their limited weight capacity.
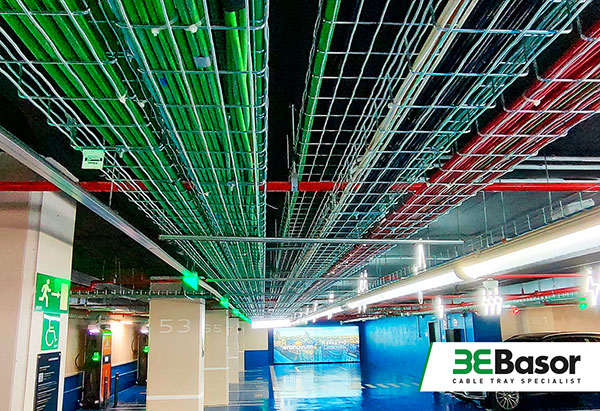
Key Benefits of Cable Trays
Using cable trays in industrial settings offers several advantages over other methods of
cable management, such as conduit systems:
● Ease of Installation: Cable trays can be installed faster than conduit systems,
reducing labor costs and installation time. They also allow for future expansion,
making it easy to add or remove cables without major modifications to the system.
● Improved Cable Organization: Trays keep cables neatly organized and easily
accessible, reducing the risk of tangling or damage. This organization is crucial in
large facilities where dozens or even hundreds of cables may run alongside each
other.
● Ventilation and Heat Management: Cable trays, particularly ladder and wire mesh
designs, allow for ample airflow around the cables, helping dissipate heat. This is
essential in environments where heat buildup could lead to cable insulation failure or
reduce the lifespan of electrical systems.
● Durability and Load Capacity: Industrial-grade cable trays are built to withstand
harsh environments, such as exposure to chemicals, UV radiation, or extreme
temperatures. Materials like galvanized steel, stainless steel, or aluminum are often
used for enhanced durability. They can also support heavy cable loads, which is a
critical consideration for high-capacity installations.
Compliance with Industry Standards
Compliance with Industry Standards
For installers and engineers, adhering to industry standards is non-negotiable. In the U.S., the National Electrical Code (NEC) provides guidelines for cable tray installation and usage. Additionally, cable trays often need to comply with standards from organizations like the National Electrical Manufacturers Association (NEMA) and the Institute of Electrical and Electronics Engineers (IEEE). These standards ensure safety and reliability, particularly in industrial settings.
Some key considerations include:
- Proper Grounding: Cable trays should be properly grounded according to NEC requirements to prevent electrical hazards.
- Load Rating: Selecting the right cable tray with the appropriate load rating is crucial to avoid structural failures, particularly in installations with heavy or high-volume cables.
- Spacing and Support: NEC specifies the maximum spacing between supports for different types of trays, ensuring stability and preventing sagging or misalignment.
- Fire Resistance Standards: Industrial cable tray installations must also adhere to fire resistance standards, which can vary depending on the environment and the nature of the installation. In fire-sensitive areas, trays should be rated for fire resistance to help contain the spread of fire and protect critical electrical infrastructure. Be sure to select cable trays that meet applicable UL 2196 or other recognized fire-resistant standards where necessary.
For more information on cable trays and their applications in industrial settings, or to explore
the solutions offered by Basor, feel free to contact us or consult our product catalog.