Today, we have the pleasure of interviewing Alejandro Jiménez, Maintenance and Plant Engineering Manager at our Basor Electric Almansa facility.
Our main factory produces over one million meters of cable tray per week, a production capacity that requires meticulous planning and constant maintenance to ensure maximum efficiency and quality. Keeping a plant of this size running smoothly is no easy task, and for that, we rely on a team that is always at the forefront of innovation.
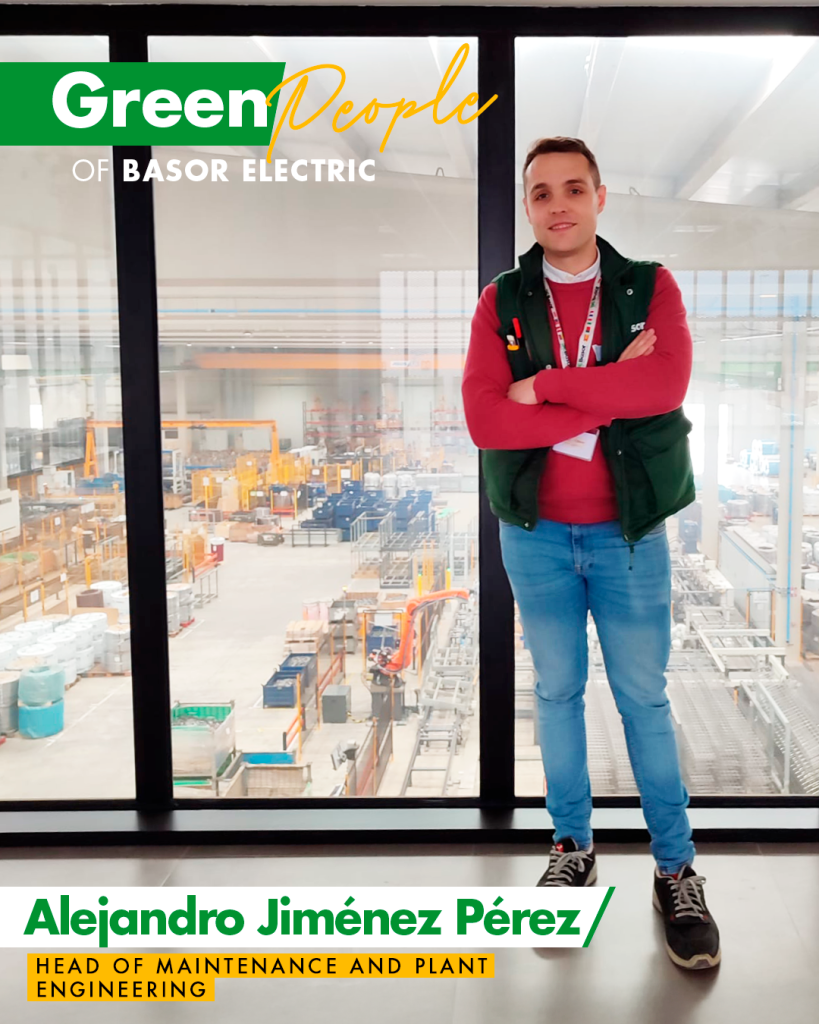
Hello, Alejandro. Tell us about your role at Basor Electric.
My job at Basor Electric, in broad terms, can be defined as follows:
- Implementing and continuously improving a more efficient and optimized management of department resources to enhance the factory’s productivity and reduce machine downtime due to breakdowns to zero. Our goal as a company is to involve the entire organization in fostering a preventive culture, allowing us to identify weak points and stock shortages that could impact safety, quality, or production.
- Participating in the design and implementation of new machinery at the Almansa plant, ensuring that we remain at the forefront of process automation and environmental management.
What are the biggest challenges you face in your day-to-day work?
The maintenance department is characterized by meticulous planning of scheduled interventions to avoid disruptions to machine productivity. However, as in any large company, the demand for corrective actions on critical machines can alter planned schedules, delaying other interventions.
Our biggest challenge is to address and resolve unexpected daily challenges in the most pragmatic and agile way possible, without compromising continuous improvement, process automation, and team training.
Another major hurdle is the diversity of machinery and processes we operate, which constantly pushes us to deepen our understanding of each machine’s characteristics and potential issues.
Maintenance is crucial in an industry like ours to prevent production stoppages. How do you manage failure prevention?
The key to effective maintenance in the company is the involvement of all employees, fostering a culture of early detection and failure prevention to minimize unexpected production stoppages.
To achieve this, we follow a structured approach that includes:
- Periodic autonomous maintenance, carried out by machine operators, who perform cleaning, lubrication, and inspections of key components to detect potential issues affecting equipment performance.
- Incident logging and communication, where any detected anomalies are reported in operational meetings. The maintenance team then evaluates the impact and determines whether immediate intervention is required or if it can be scheduled without affecting production.
- Continuous improvement cycle, in which all departments involved contribute ideas and solutions to optimize processes, increase productivity, and extend machine reliability and lifespan.
This approach allows us to keep the plant running at maximum efficiency and safety, minimizing risks and ensuring uninterrupted production processes.
Looking ahead, what projects or improvements are in progress to further optimize the Almansa plant?
The Almansa plant is a cornerstone of Basor Electric, and as such, we are committed to keeping it at the forefront of quality and safety in its processes.
In the short-to-medium term, we are implementing the following improvements:
- Full Lean System integration across all factory sections, enabling real-time monitoring and sensor-based tracking of machine productivity and failures, with the goal of implementing Predictive Maintenance.
- Automating factory supply management via SCADA, allowing us to analyze energy consumption patterns and detect potential failures in the overall system. Although we have a high degree of automation, we still have room for improvement.
- New process optimization machinery projects, all aligned with safety, quality, sustainability, and environmental impact reduction.